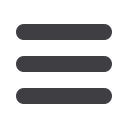
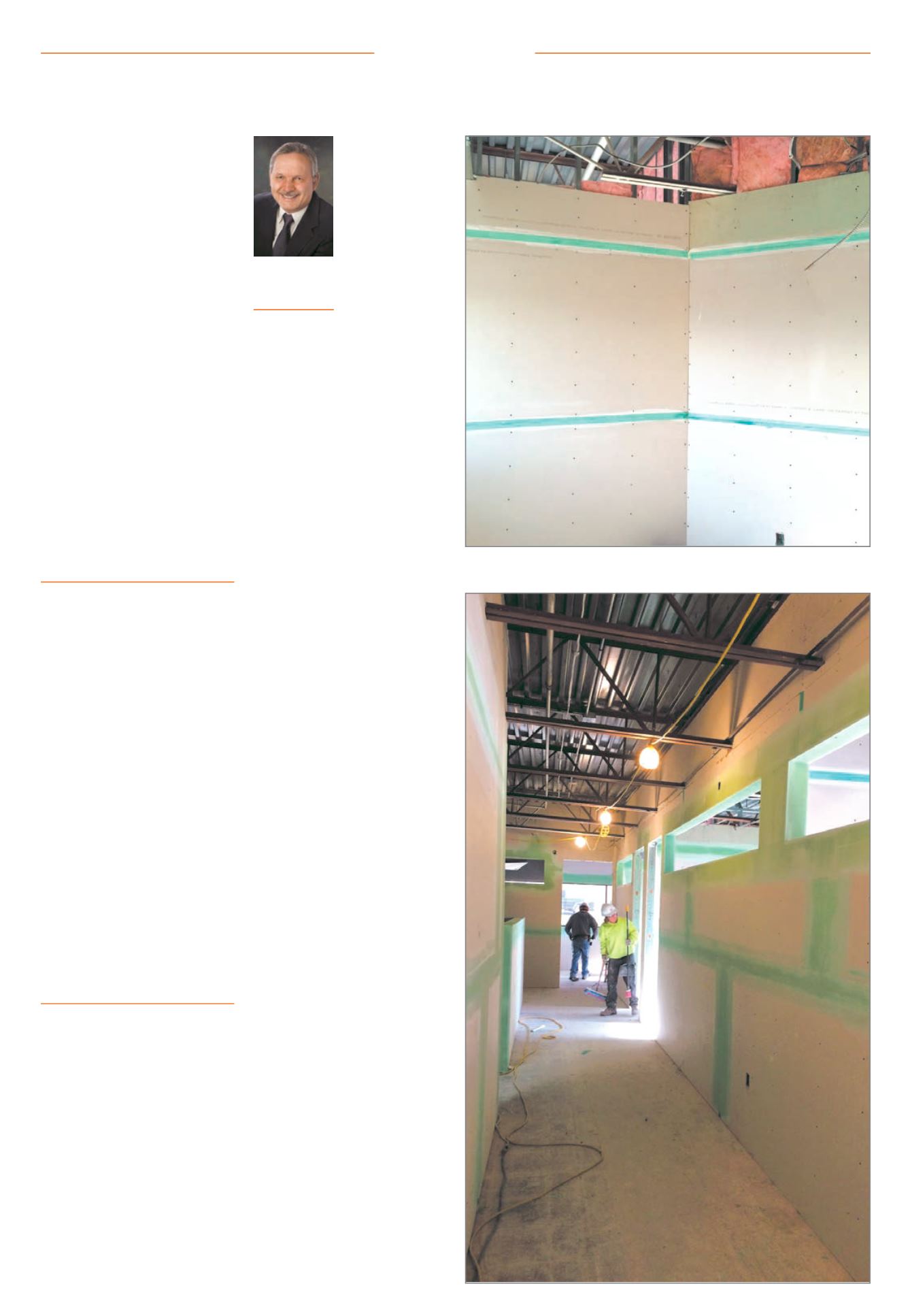
January 2015 — Multifamily Properties Quarterly —
Page 23
W
hen commercial real
estate properties are first
built, developers aren’t
thinking about how a new
owner, 10 years down the
road, needs that property to func-
tion in order to maximize profit. For
example, it is not a current concern
if multifamily properties will need
to be changed to assisted-living
properties, as the baby boomer
generation needs more care in the
next 20 years. Tenants of multifam-
ily properties have different needs
and space requirements than a
retirement home or assisted-living
facility. Maybe this should be a con-
sideration from the start in order to
secure the long-term success of the
building.
Typically, with multifamily, the
type of unit that is popular at the
time determines what the space
requirements will be. With that in
mind, there are several scenarios
that owners may face with current
buildings requiring updates. First
is demand. It makes sense that if
two- or three-bedroom units are in
demand, those would be the easiest
to rent and therefore most desir-
able for the owner. Depending on
income levels and other factors,
different size units are popular
at different times. Also, in time,
apartments may no longer be as
in demand, because condos might
become more profitable. If the
Colorado construction defect law
is changed in few years, it could be
enticing for owners to convert an
apartment building to more profit-
able condos. Another common con-
sideration is to convert lower levels
of a building into boutique retail
stores.
Often the large costs associated
with rehabbing existing buildings
for a new or future need is detri-
mental.
It would be valuable if an owner
were able to reconfigure the interior
of a building to match needs, as the
neighborhood experiences change.
A new technology makes interior
reconfiguration a reality. A former
Gensler architect and professor at
Texas A&M Univer-
sity has developed
a demountable
drywall joint tape
called Green-Zip.
This tape is impor-
tant because it
creates interior
versatility.
If you think
about the way
the interiors of
buildings are con-
structed, walls
are set into place
using studs and head rails. Then the
doors, windows, plumbing and elec-
trical are added. Drywall sections
are put onto the frame to connect
and cover up all of these items that
make up the wall.
Conventional drywall joint tape
is installed and seals access to the
entire wall, both inside and out.
It seals so well that when some-
one wants to remodel or even do
a plumbing repair, the only choice
has been demolition (hammers
and saws) and starting over with
new materials. This is very expen-
sive for the building owners. It also
accounts for 23 percent of garbage
in construction landfills, according
to the U.S. Environmental Protection
Agency. With a removable drywall
joint tape, materials can be reused,
including the drywall. Once the
drywall is removed, studs can then
be moved, allowing for the space to
be reconfigured. The same drywall
can be put back up to create that a
new space using the same materi-
als. Reconfiguring the interior saves
$110 per lineal foot, or $1,100 sav-
ings for every 10 feet compared
with demolition costs, according to
a Turner Construction case study.
Time and labor costs are also sig-
nificantly less.
Also, according to a Leadership
in Energy & Environmental Design
case study, demountable drywall
tape diverts 70 percent to 90 per-
cent of the building from landfills.
If a building is working toward Gold
LEED status, demountable tape can
contribute up to five LEED points.
“It’s encouraging to see new tech-
nology and practices that promote
both building deconstruction and
landfill construction waste diver-
sion,” said Brian Dunbar, LEED fel-
low, executive director at Institute
of the Built Environment.
The Internal Revenue Service
offers tax benefits because the
demountable dry wall tape makes
everything associated with a non
load-bearing wall pass the test
and become personal property.
This changes the materials from a
39-year to a five-year depreciation.
For the investor, this means an
additional 8.1 percent return on
equity, according to Real Estate
Review. For companies using their
own building, McGladrey account-
ing says that the tax benefits for a
profitable company is equivalent
to saving between $3 and $10 per
square foot of floor space.
The self-adhesive tape can save
time and labor because no auto-
taping tools are needed for the
first mud coat and there is no four-
hour to two-day drying time. All
of these benefits have an upfront
cost of $1 to $1.70 per sf of floor
space. A Barry Lynch, IFMA Fellow,
case study shows return on invest-
ment to be 7:1. The new industry of
changeable buildings is born with
a simple idea of demountable dry
wall tape.
s
Reconfiguring interiors using new technologyTechnology
Les Simpson
President, Deferred
Tax Benefits,
Denver
Green-Zip drywall tape adheres to drywall in the same fashion as regular tape but
without the long drying time.
The removable drywall tape is used to be able to reconfigure spaces using the same materials.
‘It’s encouraging
to see new
technology
and practices
that promote
both building
deconstruction
and landfill
construction
waste diversion.’
– Brian Dunbar, Institute of the
Built Environment